Simple Rack Changes Can Yield Powerful Rewards —
The explosion of Internet of Things (IoT) devices, and growing consumer expectations of high-speed broadband data anytime, anywhere, and everywhere, put increased pressure on data networks and infrastructure. To deliver this ever-increasing deluge of data, 5G is launching to provide these services wirelessly. Higher cable speeds (can you say "10G"?) and FTTX (fiber-to-the-business/node/home) are being deployed to support this 5G evolution. One can expect more changes in the coming years, all driven by our hunger for more, and faster, data.
Architectures are also changing, as network operators push data processing closer to the edge to reduce latency and increase Last Mile bandwidth. Whether C-RAN or remotePHY, these new architectures will someday themselves be replaced as new technologies emerge.
After all, when it comes to investment in technology, decisions are always made on the bottom line. What generates more revenue and more profit? Data.
InvisiLight® Solution for Deploying Fiber
April 2, 2022Go to Market Faster. Speed up Network Deployment
April 2, 2022Episode 10: Fiber Optic Closure Specs Explained…
April 1, 2022Food for Thought from Our 2022 ICT Visionaries
April 1, 2022A Powerful Change
Behind the scenes, power within the network has been pressed for more capacity, while power architectures have had minimal evolution. -48Vdc is still the pre-eminent architecture for myriad reasons, including efficiency (fewer voltage conversions), low voltage safety, huge legacy infrastructure, and ease of battery backup. There’s been enhancements in some areas, such as more efficient rectifiers and new battery chemistries, but the basic architecture remains.
For example, DC power tertiary distribution is widely used in telecom and cable facilities. High-current cables are routed from a main DC rectifier plant to the equipment rack, in which 1 or more power distribution panels resides at the top. This power panel then distributes power to multiple, separately protected circuits feeding individual equipment within the rack (rather than having each equipment’s power routed all the way from a distant DC rectifier plant). This equipment can be servers, routers, switches, radios, or other telecom or data equipment.
It is THIS equipment that generates revenue, not the power panel. Clearly, data is king. Data is what the customer buys, not power. So how can we get more value for the network operator in this architecture? What are the challenges that can be mitigated by looking at the power infrastructure?
Customers need more space for traffic-carrying (i.e., revenue-generating) equipment. They need fast deployments for expansion and upgrades, and need insights into power consumption (efficiency) and pending failures (proactive mitigation).
New design approaches can reduce rack space, and streamline new installations and future retrofits. Monitoring and reporting capabilities can provide enhanced power monitoring for better energy efficiency analysis, and enable proactive response to mitigate failures before they occur. Something as simple as a fresh look at top-of-rack, tertiary DC power distribution can provide opportunities for improving facility space utilization, speed of deployment, and intelligent monitoring.
Simply Impactful
AC power (120Vac) has always been associated with a plug connection, because AC power is the ubiquitous power solution in our world. However, DC power hasn’t had the benefit of a common connector, so the telecom DC world still relies on permanently fastened lugs. This is still important for technical reasons at high current connections, as it is in the AC world.
However, other than standardization (which will evolve), connectorizing the output connections on a DC panel can provide some easily obtained benefits.
Benefit #1: DENSITY
As mentioned, the standard legacy method of connecting equipment to the top-of-rack DC power distribution panel has been to use lugs. With rear-facing screws or studs, this requires the cables to come straight down (See Figure 1.), interfering with any equipment immediately below the power panel. It is typical for users to simply leave this rack unit (RU) empty.
Figure 1. Traditional lug connections.
By implementing connectors on the output power cables, cable routing can now be accomplished parallel to the floor (See Figure 2.), allowing equipment to be installed directly below the power distribution panel. Installers can then bring cables down to equipment, or route to the side of the rack or cabinet, with service loops that do not interfere with adjacent equipment.
Figure 2. Connectorized output cables.
This space-savings can extend beyond the rack to the facility, depending on scale.
Benefit #2: INSTALLATION SPEED AND SIMPLICITY
Connectors can make installations faster and simpler, when compared with lugs. A properly designed connector installs on a cable simply, with standard tools, similar to a crimped lug. That’s where the similarity ends. The lug requires a screw to be removed from the panel, inserted through the lug, then re-inserted into the panel, without dropping, stripping, or breaking the screw. The same is true for stud inputs using a nut. It also requires 2 such lugs per power output.
With a connector, a single tool-free connection is made. A properly designed connector also ensures proper polarity, and in the case where a cable is installed on the wrong circuit, it is quickly moved to the correct circuit.
Where a cable is fabricated by the cable manufacturer, or assembled off-site, technicians who may not be familiar with power can easily and safely install the cable without the specialized training needed to properly terminate a cable in the field.
Customers are currently integrating DC power panels with connectorized outputs. Though some are unique to particular vendors, the industry is likely to develop common connection standards around DC power, and equipment vendors are well advised to ensure their connector solution is future-proof and not proprietary.
Sensor Integration
Just as data is king for revenue, it is also king when it comes to managing a network. While the data network is constantly monitored for performance, ensuring traffic is flowing well, the power portion of the network has typically been passive, and monitoring has been limited to whether a circuit is operational or tripped.
Advanced power management requires adding quantitative monitoring of voltage and current at the circuit level, allowing operators to understand their power consumption, and to develop proactive response. Integrating additional sensors, such as temperature sensors, extends monitoring capabilities to other relevant network metrics.
Current sensors on each output circuit of a power panel allow monitoring of energy consumption on each individual circuit. Voltage sensors on the panel allow monitoring of voltage at the top of the rack, which can be critical for long cable runs that may introduce voltage drop, resulting in lower voltage at the rack than that being reported at the main DC distribution plant.
Where additional sensors, such as temperature sensors, are integrated into the top-of-rack panel, integrators have access to additional data such as top/bottom of rack temperatures, or cold-aisle/hot-aisle temperatures, without having to install a separate environmental monitoring system.
Monitoring capabilities can be as simple as setting alarms at particular current, voltage, or environmental thresholds, or as advanced as allowing retrieval of specific quantitative measurements to track power conditions over time.
5 Areas to Track
Area #1. Alarm thresholds allow proactive responses to pending issues in a facility. Current monitoring can notify a facility operator of a pending over-current situation before the fuse or circuit breaker opens, allowing the operator to solve a pending issue before they lose power to the equipment.
Area #2. Voltage monitoring provides insights into potential issues with voltage drop that may develop as more equipment, or different higher-power equipment, is installed at a later date, over-taxing the original cabling capacity.
Area #3. Temperature monitoring can provide insights into HVAC performance at the rack level, that may not be monitored by an overall facility HVAC control system.
Area #4. Live quantitative data provides trending information for operators. This data can be useful for energy-efficiency studies, a topic gaining significant attention in recent years. Actual current consumption data is very valuable for colocation sites, where tenants may be charged for power utilization by the landlord, whether based on time-of-use (becoming more frequently used by utilities to limit overall grid load at peak times), or simply aggregated kWh energy consumption.
Area #5. Data retrieval can also reveal trends in equipment power consumption based on traffic or pending equipment issues. In an actual situation, an operator was using a server shelf with multiple independent power feeds, each feeding an individual blade server. They observed over time that the power consumed at each feed (i.e., each blade) varied considerably, while the total of the 8 feeds varied only a little. This was diagnosed as a weakness within a few of the blades, such that they would process less traffic under certain conditions, in which case some of their load would be taken by adjacent blades; the problematic blades would later recover and accept more traffic, reducing the load on adjacent blades. This manifested itself in wide swings of power consumption on a per-blade basis, unrelated to total traffic through the blade shelf as a whole. This allowed the operator to pay closer attention to the performance of this server shelf, and to develop plans to replace those blades prior to failure.
Like this Article?
Subscribe to ISE magazine and start receiving your FREE monthly copy today!
Invest in Powerful Data
When installing new top-of-rack equipment, whether due to launching greenfield facilities or expansion and upgrading of existing facilities, the incremental expense to add high-value features such as connectorized outputs (for increased equipment density, and faster deployments and upgrades) and monitoring (to add intelligence to the non-data physical network environment) can have lasting benefits that far outweigh the additional cost.
About the Author
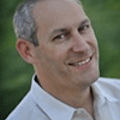