Effective Strategies for Launching Cable Landing Stations
"Understand this: any cable landing station deployment is a race against the cable itself. A ship pulls and places the cable under the sea from the origination point to the end point, and that ship isn’t cheap.
It’s tempting, as our personal lives become increasingly wireless, to assume the same is happening in the world at large. We have wireless phones and Internet, after all, as well as printers, DVRs, sound systems, streaming devices, headphones and, well, you get the picture. Wires are something our kids trip over when visiting Grandma and Grandpa’s house.
Emerson Network Power engineered and deployed this modular cable landing station with unified infrastructure for Hibernia Networks. This landing station, located near Halifax, Canada and its sister site in the United Kingdom house opposite ends of a transatlantic submarine cable.
That’s all true, but the massive amount of voice, video, and data being moved around the globe is too much for satellite transmission alone. Instead, ultra-high-bandwidth submarine fiber cables stretch from continent to continent, connecting the world — and more of these cables are being laid under the oceans every day. According to TeleGeography’s Submarine Cable Map (www.submarinecablemap.com/#/), as of February 23, 2016, there were 342 of these submarine cables — nearly twice as many as in 2012, which is an indication of just how fast these international networks are growing.
At either end of these cables are facilities called, appropriately enough, cable landing stations. The cables emerge out of the depths into these seaside enclosures, which come in all shapes and sizes. Some act more or less as a junction box, powering the cable and allowing its signals to be routed to various points via additional fiber. Others are larger, and act as telecommunications hubs or small colocation facilities, complete with extensive computing capabilities. There is no single blueprint for a cable landing station, but there are some consistent requirements influencing design and construction practices — none more ubiquitous than a need for speed.
Don’t Water Down Your Options
Understand this: any cable landing station deployment is a race against the cable itself. A ship pulls and places the cable under the sea from the origination point to the end point, and that ship isn’t cheap. In fact, at a cost of up to $200,000 per day, the ship often becomes the most expensive part of the project. If the cable reaches the end point and the landing station isn’t ready, the meter continues to run.
According to TeleGeography’s Submarine Cable Map (www.submarinecablemap.com/#/), as of February 23, 2016, there were 342 of these submarine cables — nearly twice as many as in 2012, which is an indication of just how fast these international networks are growing.
Organizations manage this in various ways. Some try to plan far in advance, padding construction timelines to ensure the building is ready when the ship arrives, but this can carry its own risks. Padded timelines can lead to padded bills, and weather can wreak havoc with even the most conservative construction plans. More importantly, elongated timelines simply aren’t realistic in most cases. These cables are carrying critical data, and the whole point is to get that data from Point A to Point B as fast as possible. The companies commissioning these projects have little patience for deliberate construction schedules.
With that in mind, alternative construction methods ensuring faster deployment are emerging as preferred choices. Prefabricated design can reduce deployment timelines by 40 percent, shaving months off traditional approaches. Additionally, the vast majority of prefab construction and assembly happens in a factory setting, ensuring no weather delays. The only on-site requirement is digging and laying the foundation — which can be done early, as the prefab modules are being prepared — and the final delivery and installation of the modules. We’ve deployed prefab landing stations at both ends of a cable within six months of project launch — much faster than any bricks-and-mortar project. If speed is the primary driver — and for cable landing stations, it usually is — prefab is an obvious choice.
Prefabrication also allows the structures on either end of the submarine cable to mirror each other while still being customized to meet local requirements in the countries where they reside. A transatlantic cable connecting landing stations in the United Kingdom and Canada, for example, may share the same basic design but will certainly require adjustments to accommodate different standards for the respective regions. Building the modules that make up those landing stations in a factory setting makes that sort of "customized standardization" easy, cost-effective, and repeatable.
Staying Above Water in Terms of Network Reliability
The benefits of prefab for cable landing stations extend beyond speed of deployment. Landing stations are, by definition, coastal installations, and that reality carries with it certain complications. These are harsh environments, and these facilities will be buffeted by sand, salt, wind, and rain. The oceanfront air is highly corrosive and potentially destructive to the structures and to the electronics enclosed within.
That presents multiple problems for traditional construction practices. We’ve discussed weather delays already, but even under optimal coastal conditions, construction is going to expose building materials to the salty, corrosive air. It’s unavoidable.
Prefabricated structures are engineered and assembled in a climate-controlled factory, pieced together far from the corrosive elements present at seaside. There is no moisture in the joints and no wind to introduce sand or salt into the modules as they come together. The factory environment enables rigorous testing to ensure the integrity of the structure. Not only is the process itself immune to the elements, it ensures the finished product provides the best possible protection — from tight construction to paints and coatings unaffected by outside conditions during application.
Of course, the coastal environment impacts more than just construction. It impacts network reliability. Thermal management is critical in these facilities, and the use of outside air is not an option for obvious reasons. Indirect evaporative units can maintain temperature and humidity points suitable for sensitive electronics without introducing corrosive air into the unit.
Ultimately, cable landing stations are no different than any other computing or telecommunications site in today’s market in one important way: they are evaluated based on performance.
Certainly, no 2 landing stations are the same, and there is no one-size-fits-all solution for every deployment. But there are some consistent requirements in this space that lend themselves to prefabricated design, increasing the likelihood of smooth sailing for what can be a complicated project.
About the Author
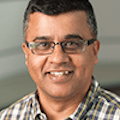