Latest from Columnist
The following came from an interested reader, and may be an issue you’ve faced. I’d like to hear your comments!
Dear Mr. McCarty:
I have been working in the area that is addressing fiber-to-the-node and fiber-to-the-home. In conversations with several of our customers, the question regarding sealing current has come up. In their application of naked DSL (just DSL no POTS voice) they are concerned with corrosion that can cause noise and circuit unbalance that can affect the data rate that they can use and the reach they can obtain. I am looking for information to see if this is a problem on only certain copper loop lengths. Is there a minimum amount of sealing current to keep the line clean, and how often the current needs to be present? I would appreciate any information.
Thank you for your time.
Dear Reader:
Thank you for your readership and for this interesting question.
Loop sealing current is better known as wetting current or fritt current. Wetting current is the minimum amount of DC current necessary to keep a mechanical switch contact on a dry loop in good health. Typically, 1-20 mA in copper wire loops. If a mechanical switch contact is operated with too little current, the contacts tend to accumulate excessive resistance and may fail prematurely. Wetting current is widely used in the telecommunications industry to solve oxidation of any switch or splice on a dry loop.
Wetting current or loop sealing current mainly addresses all-digital services on dry loops, unlike services with underlying POTS (ADSL, for example) that inherently provide wetting current by means of off-hook loop current on the POTS line. It is defined in the Belcore and CCITT Layer 1 specifications as a low current (1-20mA) DC current applied to the copper pair at the U interface.
It serves 2 purposes:
1. To reduce oxidation at line splices and mechanical switches.
2.To provide a troubleshooting aid in the field. (You can use this also for indications of connected lines.)
InvisiLight® Solution for Deploying Fiber
April 2, 2022Go to Market Faster. Speed up Network Deployment
April 2, 2022Episode 10: Fiber Optic Closure Specs Explained…
April 1, 2022Food for Thought from Our 2022 ICT Visionaries
April 1, 2022Here is where wetting or sealing current comes into play: each port on an office channel unit (OCU) interface contains a DC power supply to provide sealing current. Each power supply is completely isolated from other circuitry. Sealing current is also required to perform a remote loop back. When the channel service unit (CSU)/data service unit (DSU) loop back is selected at the system console, the remote loop back is performed by reversing the sealing current direction to the distant CSU.
In the old telephone days, leased line circuits for data were a relatively new invention, and when they first began appearing they created problems for test board personnel. These leased line circuits were the only circuits around that did not have some kind of high voltage applied to the line at least once in a while, and it became apparent that it was possible for that condition to allow these circuits to build up a charge on the line that would cause the circuit to fail.
Usually the first person to do anything to the circuit would also cause the problem to disappear with no reason. Just plug in a test set, and everything started working. This was very baffling. However, it wasn’t always that easy. And some test board people learned that before testing such problems it was a good idea to "pre-condition" the line.
Old 2-wire test boards had a cord to which ring voltage could be applied. The cord would be jacked into a circuit, and the switch flipped to "RING" a couple times. That most always worked. Today most leased lines using cable facilities are equipped with sealing current to prevent that problem. It applies a relatively small voltage (around 24 VDC) to the cables and allows 10-15ma of current to flow at all times.
That being said, when is wetting or sealing current needed?
Situation #1. When mechanical connectors with composition other than copper that causes galvanic corrosion in cable splices. All of today’s insulation displacement connectors (IDCs) do not have this problem. So, sealing current should not be needed for splice continuity.
Situation #2. Some older splices, especially in feeder pulp cables, still have unsoldered twisted splices. Rather than use sealing current on these splices it is advisable to re-splice the cables with IDC connectors.
Situation #3. Moisture intrusion in splices causes electrolysis. Don’t concern yourself with this. If there is water in splices, the infrastructure provider has other problems and the splice must be repaired.
Situation #4. Some end-user equipment requires sealing current for operation and testing.
Situation #5. Some mechanical switches require sealingcurrent to prevent oxidation and malfunction.
This is as much as I know of this interesting topic but I’d love to hear more from you about your thoughts.
Signing Off
Each month as I sit down to consider what to write about in my column, my biggest hope is that I come up with something that is helpful to at least a few technicians. If you have ideas on topics you’d like to discuss, please email me with thoughts about compelling issues. And if you have questions, you can reach me at [email protected] or text or call me at 831.818.3930. I’m here for you!
Like this Article?
Subscribe to ISE magazine and start receiving your FREE monthly copy today!
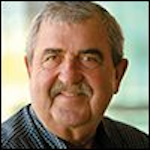