Latest from Columnist
Troubleshooting low count cables and drops with today’s test equipment —
I received an email from a field technician about a problem he was having with the fault location features of his multi-function test set when using the RFL, Open Meter, and TDR functions. He stated that the measurements were fairly accurate when using the manufacturer’s settings on cables that were 25-pair cables and larger. When measuring the distance to a fault using the manufacturers settings on small count cables such as a 6-pair cable, the measurements were inaccurate.
Field technicians use many types of test equipment or multi-function test equipment to identify and locate DC type faults in today’s outside plant environment. When the fault is in the telephone cable, not in the house or the Central Office (CO), the fault is usually in the distribution plant. Experience has shown that if a customer has a problem today that was not there yesterday and no other neighboring circuits are affected, that problem will be within a few thousand feet of a customer in a terminal, access, or pedestal.
The typical fault that disrupted service is a shorted, grounded, crossed, crossed-battery, open, going open (series resistance), or a capacitively unbalanced cable pair. These faults are identified with initial tests, and are located with a resistance bridge, an open meter, or a Time Domain Reflectometer (TDR).
These fault-locating meters are set to the parameters of the cable being tested by the test set manufacturer, and will error a percentage due to cable design. For example, when measuring the distance to a short, ground, cross, or crossed-battery, a resistance bridge converts linear wire resistance ohms to feet based upon gauge, temperature, composition, and the helical design of the cable.
If the field technician sets in the correct cable gauge and temperature into the resistance bridge, the test set will measure within 1% to 3% of the fault, depending upon the size of the cable. Any error in temperature will increase the total error. A measured distance to fault of 1,000 feet with a resistance bridge is somewhere from about 970 feet to 1,030 feet from the test set. Add a 10-degree temperature error, and that increases the error from 950 feet to 1,050 feet.
InvisiLight® Solution for Deploying Fiber
April 2, 2022Go to Market Faster. Speed up Network Deployment
April 2, 2022Episode 10: Fiber Optic Closure Specs Explained…
April 1, 2022Food for Thought from Our 2022 ICT Visionaries
April 1, 2022That’s all well and good for finding a terminating fault that occurs in an access such as in a buried pedestal or in an aerial terminal. However, I don’t expect a technician to go 50 feet from a pedestal and dig a hole or open the cable sheath on an aerial cable 50 feet from an aerial terminal when looking for a terminating fault. I would hope that the technician would look in the nearest buried pedestal or aerial terminal first, and more than likely would find the terminating fault.
The problem occurs when a field technician has to dig a hole or open the sheath of an aerial cable to find multiple faults in a section between aerial terminals, or to find multiple faults between buried pedestals or in a section of buried cable. That’s when actual known parameters are important.
When analyzing bad sections of telephone cable based upon input from a resistance bridge, an open meter,
and a TDR, proper settings must be programed into the test set depending on the type of cable in the section. Set the gauge and temperature of the section into the RFL feature of the test set. Select air-core or filled cable into the open meter function. Set the proper VP into the TDR function.
There are basic requirements to test the section. First, the actual section length must be known. Any error in the actual engineering wheel distance and the technician input will skew the analysis of the section. The actual cable temperature must be entered into the resistance bridge. Resistance bridges will give a fairly accurate distance between terminations if the gauge and temperature are correctly set.
If the actual section length is known and the resistance bridge footage compares with the actual section length, all is well. Any difference, longer or shorter, will indicate a possible gauge change, a temperature change, a slack loop, or an unknown load coil.
The TDR measurement, when set to the proper velocity of propagation (VoP), should agree with the actual section length. Any increase in distance occurs only when there is water in air-core PIC cable. Knowing the percentage of increase will indicate the approximate amount of water in the section. Then, looking from each end, the TDR will show where the water starts from each end. If this information agrees with the percentage, the water is confined to one spot. If the start from each end is longer than the percentage, pockets of water or moisture are present.
TDR velocity of propagation settings from the test set manufacturer are fairly accurate when measuring the distance to a fault or event in 25-pair cables and bigger. In order to use the section analysis tool, the exact TDR VoP of 1-pair drop, 2-pair drop, 5-pair drop, 6-pair drop, 6-pair cable, 11-pair cable, 18-pair cable, and so on, must be established before accurate section analysis can be done.
A good example is 22-gauge filled 25-pair or larger telephone cable. The average VoP setting for 22-gauge filled cable is .640. The setting for a 22-gauge 6-pair Beldon or Essex filled service drop is .629. If the .640 VoP were set and the footage were entered and compared to the actual distance, my section analysis tool would indicate water in a filled drop. I don’t think so.
Open meters are also programmed for 25-pair cables and larger. They are programmed for air-core and filled cable on tip- or ring-to-ground measurements. A good example for an open meter setting is .125 microfarads for air core cable and .134 microfarads for filled cable. The open meter setting for a 6-pair Belden or Essex drop is .143 microfarads per mile.
If the .134 microfarads setting were used, the difference between the measured footage and the known section length would indicate a gauge change or an inaccurate actual distance of the drop.
The crux of this is a database must be established on known lengths of telephone cables when using an open meter or a TDR for any fault locating on cables smaller than 25-pair. If these settings are not used in fault locating on cables smaller than 25-pair, the test sets will indicate the incorrect footage to the fault.
If you plan on fault locating on small paired cables less than 25-pair, go to your cable yard, take known lengths, more than 100 feet of every kind of cable you use, and build that database. Then, and only then, can DC type faults be located and sections properly analyzed.
Like this Article?
Subscribe to ISE magazine and start receiving your FREE monthly copy today!
Signing off
I hope this information is helpful to some of you — and if so, let me know. If you would like to add more to this column or if you have questions to what I’ve written, let me know: [email protected] or 831.818.3930.
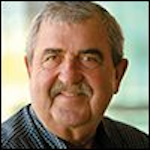