Latest from Network Reliability/Testing & Assurance/Cybersecurity/Safety
Moisture Diffusion in Underground Pulp Cable Networks
During a phone call, a cable maintenance supervisor from a large metropolitan area described a cable maintenance problem he had been recently encountering when qualifying pulp cable pairs for power pairs.
When testing any cable pairs for potential power pairs, the pair must test less than 10VAC tip to ring, tip to ground, and less than 3VDC tip to ring, tip to ground, and ring to ground. The insulation resistance must test greater than 100 megohms tip to ring when applying 500VDC to the pair with an electrical insulation test set, and greater than tip and ring to ground when applying 250VDC. The pulp cable in question would not pass. (Note: The only electrical insulation tester I’ve used is Megger but there are likely others out there.)
From his comments, I determined that the symptoms pointed to moisture diffusion in several large pulp insulated cables. This problem can be very, very costly and can have a major impact on providing quality customer service; however it has little effect on pulp cable pairs for use as power pairs.
I turned to Bob Coker for his description of diffusion of moisture into pulp cables. He is an expert in maintaining the copper infrastructure, especially pulp cables under air pressure.
Bob stated:
I’ve been in the business more than 52 years and spent much of that time dealing with cable maintenance and cable pressurization. A lot of my time was spent in hot, humid environments — the perfect environment for cable moisture problems that can cost companies multi-millions of dollars. I hope the following overview will help you consider the issues and develop a roadmap for addressing these issues.
What Is Diffusion?
A good definition of diffusion found in the dictionary states that diffusion is a process of intermingling molecules as a result of random thermal agitation. Today, due to the various environments where pulp cable networks exist, we are beginning to experience the effects of diffusion.
History of Cable and Moisture
Pulp insulation has been used to insulate conductors used in telephone cables dating as far back as Alexander Graham Bell. Pulp provided a good quality insulation and dielectric between the conductors, allowing a cable with as many as 3,600 pair to be manufactured with an outside cable sheath diameter measuring less than 4 inches.
During the cable manufacturing process, it was very important to ensure that any moisture absorbed in the pulp insulation was removed before the outside sheath cabling jacket was installed on the conductor subunits making up the bundled cable core.
The moisture removal involved a very thorough 3-step process, which included placing the unjacketed cable bundle in a large domed type oven and placing a high voltage on each of the subunits. Heat and vacuum were then applied and any moisture that was introduced in the insulating or cable bundling process was thoroughly removed. After this process was completed, the outside sheath cabling jacket was then installed.
In the early 1950s, plastics were introduced and low-density polyethylene was selected as a replacement for lead as the outside sheath cabling jacket. Low-density polyethylene provided a very good barrier against moisture intrusion up to a temperature of approximately 60 degrees F. Low-density polyethylene has a diffusion rate that nearly doubles every 10 degrees above 60 degrees F. This normally would not present a problem as long as the underground conduit routes did not reach temperatures much above 60 degrees F.
There are utility holes in the Southwest where temperatures have been documented in the middle 90-degrees-F range, and high cross battery troubles have been encountered as a result of moisture diffusion. Humidity readings were taken on air samples from the splice cases, and various amounts of humidity have been recorded. The cables in these routes were pressurized and maintained well above the 5.0 psi minimum requirement for underground exchange cable.
Stalpeth cables manufactured prior to 1980 had a soldered longitudinal seam on the steel turn plate. This soldered seam had various places that did not get completely soldered due to contamination, or poor tinning, etc., allowing minuscule amounts of moisture molecules to diffuse through the low-density polyethylene cable sheath as temperatures exceeded 60 degrees F.
Over long periods of time the accumulation of moisture reduces the pulp insulation quality, and leakage between the cable pairs results in cross battery type problems and service deterioration. As work operations in the cable networks and various leaks in the cable occur, the movement of air in the pressurized cable spreads the moisture out making resistance bridge measurements inaccurate.
Post 1980: Cable Improves, Moisture Remains
Stalpeth cables manufactured after 1980 have a bonded sheath, and the longitudinal seam on the steel turn plate has a hot melt glue providing better adhesion than the soldered seam provided prior to 1980. This type of cable eliminates the diffusion problem; however, moisture can be transferred from other sources.
Often utility manholes that contain water are not completely pumped and dried out before pulp cables are entered. The blower used for proper ventilation causes an extremely high level of humidity that can be absorbed like a blotter effect in the pulp insulation.
Pressurized cable networks need to be reviewed and checked to ensure that PIC cables and DUCTPIC cables are properly isolated from pulp sections to prevent permeated moisture from being transported through the nonhygroscopic core of the PIC cable section.
Properly maintained air dryers and portable type dry air sources used for buffering purposes should be inspected and verified in proper working order and not delivering moisture laden air to the cable networks.
While Bob’s brief article can’t answer all of your questions on qualifying pulp cable pairs, I hope it makes you question your processes and define new programs for dealing with diffusion. In my opinion, if it is indeed diffusion and the pair tests greater than 20 megohms tip to ring, tip and ring to ground, it will function as a power pair because the insulation will not break down.
Signing off
Feel free to contact me with questions for Mr. Coker or myself. We would be happy to look into this issue in more depth. Or if you have other copper cable challenges, let us know and we will get to the bottom of your problems — or at least we will try our best. Contact me at 831.818.3930 or [email protected].
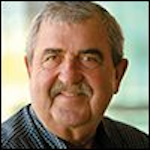