Finding Cable Trouble With a Multi-Function Test Set
We constantly hear in the field that a test set is not performing its advertised task. "My resistance bridge missed that trouble by 75 feet." "This open meter measured short or long." "The TDR indicated the fault at the wrong footage." These test sets measure footage based on the test set design engineer’s input when he built the test set, and the field technician’s input when he is using the test set. Garbage in, garbage out, folks.
When trouble is isolated to a section, and the technician decides to go after it, a conceptual picture must be built to analyze the situation and determine the problem(s) before the shovel is taken off the truck. Test equipment available to the average cable repair technician consists of a multi-function test set with a built-in digital multi-meter (DMM), a resistance bridge, an open meter, and a TDR.
When these test sets look at a cable pair, they are looking at 3 characteristics of cable: resistance, capacitance and dielectric constant. That’s all. They compare the manufacturer’s specifications against real-life cable status in the field.
The test sets are calibrated to standardized manufactured characteristics of telephone cable. For example, when a wire is insulated in the factory, the insulation extruder is paired with a spark testing unit. The newly insulated conductor passes through electrodes which detect and resist any dielectric faults (pin holes) in the insulation. This factory testing monitors the insulation resistance of the new wire. The wire is charged with a voltage, and the spark tester provides the return side of any circuit formed by a defect. Any time a technician tests a cable pair with a DMM, he’s performing the same test with all other conductors in the cable acting potentially as the other side of the circuit.
The AWG Standard
After a wire is insulated and spark tested, its conductor resistance is measured against a given length to determine if it is manufactured exactly to the proper gauge. This assures the manufacturer that the die which cuts the wire to an exact diameter (gauge) is not worn, and that the wire has not been stretched during the manufacturing process. A spool of wire (in 50,000 or 100,000 foot lengths) is placed in a temperature-controlled room for a 24-hour period, and is then attached to a precision resistance bridge. The resistance of the spool is measured and compared to a tolerance scale based on the American Wire Gauge (AWG) standard.
These standards dictate that, at 68 degrees Fahrenheit, a 19-gauge copper conductor measures 124.24 feet per ohm, a 22-gauge copper conductor measures 61.75 feet per ohm, a 24-gauge copper conductor measures 38.54 feet per ohm, and a 26-gauge copper conductor measures 24 feet per ohm. Therefore, a 100,000-foot spool of 24-gauge conductor at 68 degrees Fahrenheit should measure 2594.7067 ohms. Any resistance less than that (within a tolerance) would indicate a worn die, while a higher resistance indicates a stretched conductor.
Resistance
In the field, a portable resistance bridge measures this same conductor resistance for a given length of conductor. All such bridges are calibrated to the same AWG standard as the manufacturer’s tester. When measuring the distance to a fault, testing is based on the gauge, temperature, composition, and helical design (twist of the pairs, units, and cable during manufacture). Each of these parameters must be accurately entered into the set so an accurate sheath footage can be displayed. We’ll discuss these in order.
Gauge
Gauge is easily determined at the test site, and as long as the conductor remains in one gauge, accurate measurements can be made. Your resistance bridge would be capable of measuring to an accuracy of 1 foot in 1,000 feet of unencumbered conductor. It’s when this conductor is paired, twisted grouped and placed inside of a cable that test set inaccuracy increases.
If the gauge changes in a resistance bridge measurement, this change must be accounted for, or the measurement is inaccurate. The measurement is no longer a sheath footage measurement, but the equivalent resistance of 2 different gauges measured in 1 gauge. Using a gauge change formula, the exact sheath footage can be calculated.
Temperature
The cable manufacturing plant stabilizes the conductor to an exact temperature for testing. If a technician sets his resistance bridge to a wrong temperature, measurements will be inaccurate. This error is .00218 feet per degree of error per foot of wire measured. For example, a 10-degree error on a distance measurement of 1,000 feet produces an error of 21.8 feet.
We realize that most buried section measurements are backed up with an earth frame, but if the problem is a wet module in a buried splice, and you have the shovel in your hand, temperature is important.
Temperature changes also affect measurement. If a portion of a distance measurement is in an aerial cable, and then goes down the pole and is buried, wire temperature changes.
A temperature change must be treated like a gauge change, using a temperature conversion formula to find the exact sheath footage to a fault.
Composition
Most wire in the field is copper, but not all of it. We’ll use a 22-gauge conductor as an example of how composition affects resistance. A 22-gauge copper conductor measures 61.75 feet per ohm at 68 degrees Fahrenheit. A 22-gauge aluminum conductor measures 37.08 feet per ohm at that temperature. Aluminum doesn’t conduct electricity as well as copper, so there are less feet per ohm.
A real-world example of where a technician will run into the composition problem in the field is with "B" service wire. "B" service wire is a 2-pair drop wire that is colored red, green, yellow, and black. The drop is air-core and has an aluminum shield. The wire is 20-gauge, but steel is added to the copper for strength, which changes the resistance. To measure "B" service wire with a resistance bridge, set the gauge switch to 24-gauge, and set the temperature control 26 degrees lower than actual buried conductor temperature.
Helix (twist)
Two individual conductors are tested for any resistance unbalance, and then twisted into a cable pair. In PIC cables, each sub-unit has 25 different twists that range from 2 inches to 6 inches. For example, in all gauges, the white-blue pair has about 2 inches per twist. The old split maker, the red-slate pair is about 4.7 inches per twist in 24-gauge and 26-gauge.
The sub-units are twisted into units, tested, and the units are made into cables. Twisting the sub-units and units creates better transmission characteristics in a cable. The twist makes one unit invisible to another unit from a standpoint of capacitance or cross-talk. The lay or twist in the cable makes it flexible for placing purposes and temperature changes throughout its life.
The resistance bridge allows for this helical design. For example, if 100 feet of cable sheath were opened, and the white-blue pair removed from a sub-unit and untwisted, it would measure 103 feet in length. If the red-slate pair were untwisted, it would measure 101 feet. As you can see, this would create a 1% to 3% error, depending upon which pair a technician is measuring in a cable. The resistance bridge subtracts approximately 2% for the helix or twist of the cable. Even so, different pairs in a given length of cable measure a different footage, within a tolerance. So, you see, the best accuracy with any resistance bridge is 1 foot in 100 feet, unless each conductor is calibrated to the exact sheath footage for each measurement.
Capacitance
Mutual capacitance is a requirement in every cable specification. The manufacturer tests all cables for their mutual capacitance. The desired average capacitance for an exchange cable pair is .083 microfarads per mile or 51.6 Nano farads per kilometer. Open meters are calibrated to this capacitance to measure the distance to an open cable pair. Since this is an average, distance to opens are approximate but will allow the technician to find opens in accesses close to the measurement. If the problem is in a section, the technician must calibrate the open meter to the exact capacitance of that section for pinpoint accuracy.
Your open meter is designed to measure pairs in working cables. When the sub-unit or unit is twisted, all other pairs in all other units of the cable become invisible to pairs in that unit from a standpoint of capacitance. This means that capacitance from pairs in other units will not affect open meter measurements.
When measuring in non-working units of cable within the group the open is in, an electro-static or false shield is created by non-working units, the distance to the open pairs will measure shorter than the actual distance. This phenomenon affects only the pairs under one binder tie.
An example of this is measuring the distance to a cut cable from a terminal on the field side of the cut cable. A cut cable 400 feet from the terminal would measure 350 feet on any open meter. This effect is easily eliminated: simply ground 12 pairs in the same group (under that binder tie) and the measurement will be accurate.
Measurements to ground (ring or tip) differ in filled cables and air-core cables. In filled cables, capacitance to ground increases about 23%. To compensate for this, use the capacitance setting shown in your open meter’s operation manual.
Dielectric
The dielectric is any material used in a cable that will insulate one conductor from another or from the shield. This dielectric constant affects a Time Domain Reflectometer (TDR), as it is different in pulp, air-core PIC, and filled PIC (both solid and foam skin) conductors. TDRs are affected by the type of insulation on a cable pair, as the speed (propagation factor) of the input pulse varies with different kinds of insulation. The propagation factor must be set for each type of cable dielectric or the distance measurements will be inaccurate.
Test sets don’t miss-locate cable faults — technicians do, and it’s understandable why they might make mistakes. It’s a technical and complex issue and requires knowledge provided by appropriate training. Knowing how a cable is made and to what standards will help a technician program a test set to yield correct fault measurements.
The better informed you are, the more successful you’ll be. What you don’t know can hurt you — in time, effort, and money.
Signing off
What has been your experience with locating cable, and have you had issues that you can describe and others can learn from? Your input about this column, any other columns I’ve written, or your specific experience, drive the content of my column, so please contact me at [email protected] or 831.818.3930
About the Author
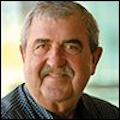