Latest from Network Reliability/Testing & Assurance/Cybersecurity/Safety
Training Field Technicians in the Past and the Present
The transition to fiber is finally progressing with more consistency. Nevertheless, copper is still around for most companies, and it requires repair and maintenance. Yet what we find is that the demands to move to cable means there is little respect and training for the copper technician.
I get it. You don’t find it critical to your long-term strategy. But that’s short-sighted. Give your copper techs the tools and training (and respect), and they will perform their role more efficiently, which means they will spend less time on each call, and that results in more money to put towards fiber.
I’ve written so many columns about the costs and time involved to dig curiosity holes, the process used by technicians who aren’t properly trained in cable location, repair, and maintenance. If you can cut the cost of truck rolls and curiosity holes by 50%-85%, isn’t that worth providing a budget to old technology and training, given it still has to operate to keep many of your customers happy and committed to you for their next-generation technology demands?
What I’ve done and what you should expect from any trainer, whether in-house or a hired contractor, is that they create programs that turn average technicians into really great problem-solvers with the right tools and standardized, proven techniques and procedures.
Turn your training into a strategic initiative that is guaranteed to deliver consistent results with a goal to developing super techs.
What’s needed to create a great training program?
If you have in-house training or hire contractors, first take a hard look at those trainers. Feel confident that they
A. have the personality, drive, and interest in training and are qualified;
B. have been in the field for a long time, and experienced many different cases of trouble, and they regularly go back into the field with the techs both to support the techs but also to make sure their own skills have kept up with changing conditions and challenges; and
C. are strategic thinkers, and can productize their training by developing programs that are repeatable, effective, and demonstrate consistent results.
In the Past
When I was hired on as a lineman with Northwestern Bell Telephone (part of the old AT&T) in the early 1960s, the Bell System Practices (BSP) which included a safety handbook that was part of my daily routine, our safety motto was No job is so important and no service is so urgent that we cannot take time to perform our work safely. The safety supervisor could show up at any job at any time.
Most new hires started on the line crew. They first went to line school for 2 weeks. They studied the BSPs, and BSP 620 to 649 covered all aspects of outside construction and maintenance, and showed a step-by-step process for any specific task. At school, they were certified in all aspects of line work, and after school was assigned to a line crew as an apprentice lineman. A line crew consisted of a line foreman, a senior journeyman, and 4 linemen. After a period of 2 years of on the job training, most were certified as a journeyman.
They then could move on to other jobs within the company such as installation technicians or construction splicing technicians. If they moved on to construction splicing they went to splicing school, and after some 13 weeks or so of splicing school were assigned to work as a splicer’s helper for a journeyman splicer. After 2 years of on the job training they were certified as journeyman splicers. After 10 or more years, a splicer could move on to cable maintenance and finally into the test board or engineering.
Maintenance splicers were schooled on DC type fault locating and cable locating path and depth, transmission testing, and noise mitigation. They were trained on the use of volt/ohmmeters, the breakdown test set for wet pulp cables, the T136 transmission test set to measure circuit parameters such as loop current and circuit loss. It also measured circuit noise, power influence for noise mitigation problems, and calculated longitudinal balance of a cable pair.
If the technician selected installation, installation school was typically 6 weeks and then a month ride along with a journeyman installer. They could move on to installation repair, business technician, special service technician, or a coin technician for pay phones. At that time, coin phones were no nickel-and-dime businesses.
Because of the complexity of the design faults, technicians with little or no training in AC/DC theory could not interpret the results, so basic electricity AC and DC training was in order. In the meantime, transmission tests were turned over to cable maintenance or engineering to be analyzed, interpreted, and repaired.
With the advent of plastic insulated conductor (PIC) cables, new test sets were in order. Companies other than Western Electric and GTE were getting into the test set business. The Delcon Corporation provided the first resistance bridge and the first open meter for PIC cables. They sold them to telephone companies with no training offered. They did come with a manual written by an engineer on acid in French, Italian, and Hebrew — who never spent a day in the field.
Telcos reacted stating that they would buy the product only if training came with it. Test set vendors responded by sending field engineers and sales engineers to do on-site training, with some success. Most test set vendors also provided a how-to video with the test set.
In 1984 deregulation blew technician training out the window. Management teams working on a number-of-jobs-in-8-hours index could not afford to have their field technicians off the load for 1 hour let alone 5 days for training.
In the Present
Complicating the issue of training is a barrage of complex new high-tech equipment: multi-functional test sets have built-in features for fault locating the copper infrastructure, digital multi-meters (DMM), resistance bridges, open meters, time domain reflectometers (TDRs), and transmission testing features along with XDSL testing. Additionally, there are constant upgrades to the test sets as new technology testing must be addressed.
Quality test-set vendors provide both on-line and on-site training for both copper and fiber test equipment. For example, one vendor provides a self-paced online training session that technicians and managers can do at their own pace. They can also guide attendees through live test sessions on-site.
It’s important to take advantage of any free resources; however, quality training must be connected to each communication provider matching their goals for training technicians and for how they will utilize the equipment. Learning the skills specific to their job will help the field technician on a daily basis.
A good training program should include a mix of the best materials, workbooks, lectures, hands-on in class, and field work. And, of course must provide training that addresses different skills and experience levels of the trainers. The training programs should be well-packaged so that if different training instructors are used, the results would be the same.
For copper training, I’ve found that ideally the techs will spend 3 days in class and 2 days in the field with the trainer riding shotgun. Additionally, coaching sessions help instill what was learned in the training. The first session would be ideally 2 weeks after training (so the techs have had plenty of field time to test their skills) followed by a session every 3 months. These sessions can be hands-on if that’s an option and affordable, or
as webcasts.
Any program should have measurable outcomes so that you feel confident in the ROI, and so that the tech knows where they may need more support. Make sure the techs complete a Satisfaction Survey after training.
Training must be a strategic initiative if you want to decrease time techs spend trying to fix a problem. This results in less down time for customers and fewer resources being spent on each job. The old "jobs in 8" which typically resulted in "cut to clear" insured more jobs were completed in 8 hours, and also insured that the plant would be a mess which, for most companies, it is. So pick the right strategic outcome!
Signing off
Once a year or even less, I write columns stressing the importance of good training programs. I know most readers prefer technical columns, but I also feel like I need to advocate for you techs who are short-changed when it comes to training! If you have questions or thoughts about this column, or other ideas you want to share, you can reach me at 831.818.393 (text or call) or email me at [email protected].
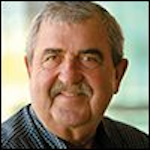