Latest from FTTx/Optical Networks
Cleaning and Inspecting MPO Connectors —
Multi-Fiber Push On (MPO) connectors have long been a staple for interconnection within data centers. They allow quick and easy connection of fiber trunks, which have become essential for high-speed technologies such as 100 Gb Ethernet. Lately, they are beginning to appear in more locations outside the data center. They’re also cropping up in multiple dwelling units and even in enterprises, connecting the data center to distribution points closer to the end users. And Fiber to the Antenna (FTTA) for 5G applications will require high bandwidth fiber, a prefect application for MPOs.
Figure 1. Single-row versions of FOCIS 5 (base 12) and FOCIS 18 (base 16) connectors. Note the difference in the key position (centered in the FOCIS 5, offset in the FOCIS 18), and pin size and spacing.
MPOs come in two Fiber Optic Connector Intermateability Standards (FOCIS). FOCIS 5 specifies 1 or 2 rows of 12 connections, while FOCIS 18 offers 1 or 2 rows of 16 connections. (See Figure 1.) Both offer the same size endface, but with slightly different physical characteristics that prevent one from interconnecting with the other — which is handy, since the fiber spacing is somewhat different, and the 2 are incompatible. MPO connectors include pins and guide holes to make sure the end faces of the fiber mate precisely. Note there are other, non-standard configurations that can support as many as 6 rows of 12 for a total of 72 fibers.
FOCIS 5 connectors are by far the most widely used. FOCIS 18 is a future-ready technology that will allow higher density but today is rarely deployed. Since high-speed Ethernet tends to aggregate 8 fibers together, many FOCIS 5 implementations use only 8 of the 12 connections — sometimes leaving 2 on each edge of the row unused, or 4 in the middle unused.
Most customers purchase pre-configured MPO cables to their specifications. There are a number of common implementations for the cables:
Pre-terminated end-to-end connections. The customer specifies the exact length of the MPO-to-MPO trunk and it is delivered by the manufacturer. In many cases, these are plugged into cassettes where the fibers are broken out into individual connections, such as LC’s.
Single-ended connections with an MPO on one end and individual unterminated fibers on the far end. This more flexible approach allows the user to splice the fiber to their connection on the other end.
InvisiLight® Solution for Deploying Fiber
April 2, 2022Go to Market Faster. Speed up Network Deployment
April 2, 2022Episode 10: Fiber Optic Closure Specs Explained…
April 1, 2022Food for Thought from Our 2022 ICT Visionaries
April 1, 2022Contamination Risk
MPO connections, like any fiber connections, are susceptible to contamination on the endface. Contamination is widely recognized as the Number One cause of fiber failure. MPO contamination is a bigger concern than on a single fiber, as a single contaminant can affect multiple links, or higher speed critical trunks.
An MPO also has many times more surface area that can collect contaminants, which can then migrate around the connector, blocking multiple connections, affecting the ability for the MPO to mate properly, and potentially damaging other MPO cables. Since most MPO cabling is either custom-made or custom-installed, replacing a damaged one is a lot more complicated than grabbing an off-the-shelf replacement.
Figure 2. A customer-supplied automated inspection image of an "out-of-the-bag" fiber. Contaminants are marked in red and blue.
And don’t think you can neglect to inspect when installing newly purchased MPO connectors from the factory. Installers report that a significant number of new, out-of-the-bag MPO trunks have enough contamination to affect performance. And even manufacturers advise that you check their work: "A speck of dust that’s invisible to the human eye can cause intermittent errors or even complete failure on a fiber optic connection," according to Mike Hughes, VP of Product Management at US Conec, a global leader in the development and supply of high-density optical interconnects, and inventor of the MTP® high performance MPO connector. "That’s why it’s essential that every fiber interconnect — even on cables straight from the factory — be inspected before it’s connected." (See Figure 2.)
So, if you’re going to address fiber contamination, and you are responsible for an installation with MPOs, inspections should be at the top of your list.
The general methodology for ensuring clean fiber connections is the same for MPOs as it is for any other fiber: any time you’re connecting a fiber, inspect, and, if necessary, clean and inspect again.
Until recently, inspecting MPOs involved using X-Y translators with a standard single strand fiber-optic microscope. Turning one knob to move from left-to-right across the fibers and another to switch between rows resulted in a time-consuming process where it would be easy to miss an endface. Thankfully, cameras designed expressly for inspecting MPOs are now offered, simplifying and speeding up the process. These models allow a detailed view of each individual fiber, and can also grade them with a Pass or Fail result based on IEC 61300-3-35, eliminating human error, although that process can take up to a minute. (See Figure 3.)
Figure 3. Automated MPO inspection screen. Note the numbering of each fiber, and indication of passing (green) and failing (red) fibers.
Automated inspectors also make it very easy to generate a report for the endface if documentation is required. Some models can provide a view of the entire endface in real time, eliminating the need for that longer automated inspection when the connector is obviously dirty, and allowing the user to see if contamination is present in an area away from an endface. Remember, that contamination can migrate to a more disruptive spot when the connector is plugged in. (See Figure 4.)
Figure 4. Cameras that display the entire endface can show potential issues such as the large particle between fibers 1 and 13. It’s not blocking anything now, but a very slight move could change that.
Pen-type (also called probe-type) cleaners designed for cleaning MPOs are the first choice for cleaning MPO cables and ports. (See Figure 5.) A cleaning cloth rotates when the cleaner is pressed to the end-face of the MPO, cleaning it. Different models are required for cleaning base-12 (FOCIS 5) and base-16 (FOCIS 18) connectors.
Figure 5. Fiber cleaning pen.
Just like with single fibers, pen cleaners are the fastest and easiest way to deal with dry contaminants, such as dust and fibers, that are the most common form of contamination. Usually a click or two is all it takes for a completely clean endface.
Wet or oil-based contaminants, such as fingerprints, are much less common, and stubborn as well. (See Figure 6.) Like a single fiber, a wet cleaning approach is recommended. However, because of their larger area and pins that can interfere with typical cleaning wipe or cube, an alternative wet cleaning approach is recommended.
Figure 6. Fingerprint oils on an MPO endface.
The first rule of wet-cleaning MPOs is to use a solvent designed for the purpose. Isopropyl Alcohol and other non-recommended cleaners can leave residue behind, and you end up with a worse situation than what you started with. The second rule is to limit the amount of solvent used.
Your trusty pen cleaner can be used for this purpose in conjunction with a cleaning wipe or cube:
• First, click the pen cleaner to advance to bring up a fresh cleaning surface.
• Second, touch the solvent pen to the wipe to make a wet spot.
• Third, touch the tip of the pen cleaner to the wet spot to moisten it.
• Fourth, use the pen to clean the endface in the normal fashion — with an extra couple of clicks to ensure the endface is dry.
Like this Article?
Subscribe to ISE magazine and start receiving your FREE monthly copy today!
Once you’ve cleaned the endface, you’re ready for the final inspection to verify that it really is clean. Don’t be surprised if you end up cleaning again — that’s not uncommon.
Once you verify that it is clean, you’re ready to plug it in. You shouldn’t have to clean it again until you unplug it. Of course, that’s not guaranteed, because someone else with less stringent fiber maintenance habits might tinker with it — without informing you!
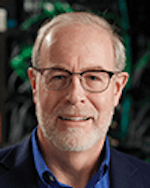