Latest from FTTx/Optical Networks
New Strategy Boosts Proactive Field Test Efficiency —
With fiber going deeper everywhere to prep the foundation for 5G, a shortage of qualified technicians who can efficiently install and test fiber is already being felt. The BT Group alone announced that nearly 3,000 new trainees will be recruited during 2019 to support its fiber deployments. The organization opened 12 new regional training centers to upskill this new workforce. On top of this, many of these new employees are completely new to fiber testing, coming from a copper or electrical background.
This shows just how important it is to have skilled technicians involved when building robust and reliable networks. Speaking of robust networks, visibility over the quality of the infrastructure is also becoming a keystone in ensuring that customer expectations are met. For existing networks, some links will require maintenance before being upgraded for faster transmissions — a cost that can get out of hand if the technicians dispatched for troubleshooting aren’t equipped with adequate testers. On average 85% of frontline technicians are equipped with light source and power meters or visual fault locators. This is sufficient to verify if a link has power and continuity, but not enough to find and identify faults, such as bad connectors.
For that, an extra truck roll is usually required with a level-2 technician equipped with an OTDR. These expert technicians are not as numerous (a ratio of 5 frontline techs to 1 level-2 expert). This means they are sought after and are less available, which in turn means that troubleshooting can be delayed for days. The impact on customer satisfaction is direct. It is important to bear in mind that dispatching a level-2 technician is more expensive for the operator or contractor.
This situation is pretty much inevitable for existing networks. But for new networks, a disruptive approach is now possible to keep unexpected costs at bay.
InvisiLight® Solution for Deploying Fiber
April 2, 2022Go to Market Faster. Speed up Network Deployment
April 2, 2022Episode 10: Fiber Optic Closure Specs Explained…
April 1, 2022Food for Thought from Our 2022 ICT Visionaries
April 1, 2022A New Approach
When dealing with new installations, service activation, and turn-up jobs, frontline technicians have 3 usual approaches today:
1. The no-testing approach.
2. Continuity validation and power level verification.
3. When an issue arises that is not easy to fix, a ticket for a level-2 technician is opened, causing an extra truck roll. When the level-2 technicians are on-site to find the faults, they either fix the issues themselves or they call back frontline crews to fix the identified issues.
A better preventive and proactive approach on-site can greatly help to minimize the number of level-2 tickets, while speeding up acceptance and even preventing eventual downtime for subscribers.
The idea is to maximize the presence of frontline technicians on-site by empowering them with the capability to validate links, and to find and fix faults. This improved approach means that level-2 technicians can be dispatched to more cumbersome jobs that really require their expertise.
By empowering frontline technicians to find and fix issues as they arise during installation, they can leave the site with the confidence that no faults are left behind. This means faster time to revenue since job acceptance and service activation are now done in a breeze.
For a typical installation acceptance job, a level-2 technician is sent to characterize the fiber by shooting OTDR traces and extracting reports. This phase often includes some troubleshooting, as previously unnoticed faulty events show up. The technician cannot leave the site with a trace that includes faulty events, so, as mentioned earlier, either the technician calls the frontline techs back to fix faults, or the level-2 technician takes care of it, overshooting the time (and costs) planned. This results in high OpEx and low Return On Investment (ROI) for one job. Validating that the link is free of faulty events before the installation acceptance test ensures that the level-2 technician is verifying events that yield results within thresholds, allowing them to close more jobs and reducing the overall number of truck rolls. This pre-validation work goes beyond speeding up acceptance. It also ensures fewer outages later on, therefore keeping better quality of service for the customer.
Seems like a no-brainer. Frontline techs should always track potential faults before leaving a site, right? Unfortunately, that’s not always what’s happening out there. One reason is that not all frontline technicians have been trained to operate an OTDR. Even with the recent improvements (such as link mapping) that make them easier to use, OTDRs still require setting up thresholds and parameters, values that may not be known to frontline technicians.
Training large crews of technicians on OTDRs is quite tedious and expensive. OTDRs will always be essential to characterize links — especially during construction — and to troubleshoot major issues, but not all jobs that are escalated to level-2 technicians require that much expertise. Likewise, equipping 5 times more technicians with OTDRs may not be something all operators and contractors can afford. And low-end OTDRs with poor specifications are not the solution.
How can a disruptive approach truly maximize the time spent on-site by frontline technicians during installation and service activation?
The solution resides in a cost-effective and simple-to-use solution that allows them to verify links and go the extra mile if issues are suspected. It must quickly display length, loss, and optical return loss of a link, while being capable of tracking faults when needed, without the need to set up thresholds. Such a solution cranks up the efficiency of frontline technicians as never seen before.
By equipping frontline technicians with this new capability, they are empowered to:
• Verify links faster.
• Troubleshoot issues with leaner methods of procedures (MOPs).
• Avoid escalation to level-2 techs.
• Avoid repeat truck rolls to fix issues.
This proactive testing approach also frees up level-2 technicians to focus on jobs that really require their expertise:
• Run fault-free OTDR traces on the first time
• Avoid fixing faults or create tickets for frontline techs to come back and fix faults
• Close more jobs per day
Such a technological capability represents a shift in the industry. What’s more, it’s also good for the ROI.
What’s the True Cost?
When it comes to investing in testing gear, you have to consider the overall cost of ownership and training expenses. How to upskill technicians without spending too much on training or sophisticated equipment?
First, look for equipment that doesn’t require knowing thresholds, testing at multiple wavelengths or interpreting traces. Look for a solution that is simple, with a user-friendly interface, to avoid extensive training.
Secondly, see beyond the buying price. To get the total cost of ownership, factor in the yearly calibration costs (plus the hassle of shipping your unit back to factory and the time it takes to get it back). These costs are often overlooked when purchasing test equipment. Shipping, clearing customs, tracking packages: all come with costs — plus the downtime of the unit while it’s away. Keep an informed eye out for equipment that does not require factory maintenance or calibration and that has field-replaceable parts (such as connectors and batteries).
Like this Article?
Subscribe to ISE magazine and start receiving your FREE monthly copy today!
An example of tools that meet the criteria described above include optical fiber multimeters (OFMs), a recently introduced category of test tools. OFMs fill the gap that existed until now in the industry in terms of empowering and upskilling frontline technicians and maximizing their presence on-site without extensive training. OFMs aim to ramp up field efficiencies with the major network transformations ahead. EXFO’s Optical Xplorer is one option to explore. It provides a qualitative assessment of the quality and robustness of a link, without having to define thresholds. It verifies links and explores further when faults are suspected. It also includes click-out optical connectors that allow field technicians to replace damaged connectors in the field.
Finally, a word to the wise: weigh your benefits in the mid- and long-term against any perceived short-term gains that might actually cost you more than you think.
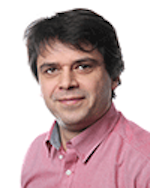