Latest from FTTx/Optical Networks
What’s New in Optical Fiber Ribbon Cable —
There’s a new generation of optical fiber ribbon cables. These designs use flexible ribbons to increase fiber density by a factor of two or more. Like any good thing, this improvement comes with trade-offs. In this article, we explain these trade-offs to help you understand whether this new technology is a fit for you.
Conventional optical fiber ribbons (or flat ribbons) have long been used for higher fiber count cables. Ribbonized fibers are easier to manage in large numbers than loose fibers. Flat ribbons can also be mass fusion spliced, which is up to 6 times faster than single fiber splicing.
Figure 1. Flat ribbons waste space in a buffer tube, and will concentrate stresses on fibers at the corner of the ribbon stack.
But, flat ribbons have a fundamental shortcoming. When cabled, a stack of flat ribbons is like a "square peg in a round hole." (See Figure 1.) Buffer tubes are generally round, which means the space highlighted in yellow is wasted. When external factors bring the stack in contact with the tube wall, it also concentrates stresses on the fibers at the corners of the stack.
Flexible ribbons solve these problems by striking a compromise. The structure that binds the individual fibers together is made looser, so a flexible ribbon can change shape without breaking apart. But, it must still hold together well enough to be handled efficiently during mass fusion splicing. Figure 2 shows a flexible ribbon (top) and a flat ribbon (bottom). Notice how the color sequence of individual fibers is maintained in the flexible ribbon without the fibers being bound tightly in place by a thick layer of matrix material.
Figure 2. Unlike flat ribbons (bottom), flexible ribbons (top) have a loose structure. This structure fits into round tubes more efficiently.
Flexible ribbons conform to the space they’re in — no more square pegs in round holes. When flexible ribbons are pressed against the inside of a buffer tube, the pressure is spread out over many fibers — not just the ones at the corners of a stack. This allows more fiber to be placed into the same space. Figure 3 shows an 864-count flat ribbon cable (left) alongside a 1,728-count flexible ribbon cable (right). The tubes on the left cable contain 144 fibers in flat ribbons. The tubes on the right contain 288 fibers in flexible ribbons. Both cables contain standard 250-micron fibers and will fit in a 1-1/4" duct. Yet, despite having twice the fiber count, the 1,728-count flexible ribbon cable is slightly smaller than the 864-count with flat ribbons.
Figure 3. A 1,728-count flexible ribbon cable (right) is smaller than a flat ribbon cable (left) with half the fiber count.
Is It a Fit for You?
Flexible ribbon cables were originally developed for Hyper Scale Data Centers (HSDCs). Most folks think of a 1,728-fiber cable as size XXL. But, it’s an entry-level fiber count in many HSDCs, where it’s common to have many such cables entering each building. These cables typically interconnect buildings without branching, tapering, or mid-span access of any kind. These 2 factors drive HSDC cable designers to prioritize high-fiber density above all else. If you’re not building an HSDC, your priorities may be different. So, let’s look at 7 differences between flexible and flat ribbon cables that may impact traditional OSP applications.
Difference #1 Ribbon Flexibility
Flat ribbons will bend on only one plane. Since they’re also twisted (to equalize stresses), this can make them more challenging to organize in splice trays. Flexible ribbons don’t have this limitation, and behave almost like loose fibers. This makes them easier to organize in splice trays.
Difference #2 Splicing Speed
Mass splicing of flexible ribbon is still much faster than individual fiber splicing. But, you should expect some loss of speed compared to flat ribbons. Because flexible ribbons are more loosely bound together, they require more care when being placed in splicing holders. A flat ribbon can be placed directly into the groove of a holder. The same technique can result in misaligned fibers for a flexible ribbon. Technicians typically "wipe" the fibers of a flexible ribbon with a thumb and index finger to bring the fibers into their proper position.
Difference #3 Splicing Tools
Flexible ribbons may interact with your current splicing tools differently than flat ribbons. Any difficulties are usually resolved with a bit of practice or some new tools. Consider testing some bare ribbon samples before scheduling a time-sensitive installation.
Check your existing ribbon holders to see if they meet your expectations when splicing flexible ribbons. Some fusion splicer manufacturers offer holders optimized for splicing flexible ribbons. They may save time or even be necessary to avoid fiber slippage during heat stripping.
Some legacy heat strippers are not hot enough to cleanly strip a flexible ribbon in one pass. Some vendors have released new models with higher temperature settings to address this issue.
Difference #4 Cost
Flexible ribbons are a new technology. There’s not as much production capacity, and flexible ribbon production is less efficient than traditional flat ribbons. The risk of production scrap also increases with higher fiber counts. So, there is a cost premium associated with flexible ribbons — particularly in the highest fiber counts.
Difference #5 Fiber Diameter
Most cablers are using 200-micron fibers for counts of 3,456 and above. There are splicers for 200-micron ribbons, but they’re relatively new. If you want to splice onto a legacy cable with 250-micron fibers, you’ll need a work-around to do it. Luckily, most flexible ribbon cables with counts of 1,728 or less will contain standard 250-micron fiber.
Difference #6 Cable Handling
Switching to flexible ribbons may impact your choice of cable structures. Cables with strength members embedded in their jackets will bend only in one plane, and are more difficult to coil. They can also be harder to open.1 Check with your cabler to see what options are available.
Difference #7 Buffer Tubes
Cable Outside Diameter (OD) can be reduced by eliminating buffer tubes. However, buffer tubes save time and simplify fiber management when prepping cables for splice closures. Buffer tubes also provide additional fiber cut protection when opening the cable jacket.
Summary
Flexible ribbon cables offer dramatic improvements in fiber density that allow more than twice the fiber count in the same duct space. If you need to maximize fiber count in a duct, they may be your best option. However, some adaptation is required, and there may be time penalties during handling and splicing. The available cable structures vary a lot. So, you should explore your options. For counts of 3,456 or higher, 200-micron fiber is common, which may require dedicated splicing equipment.
Bibliography
1. So Many Fiber Questions by J. Fitz, ISE magazine, August 2017.
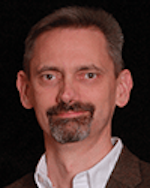