Latest from FTTx/Optical Networks
How to Resolve 5 Recurring Problems —
Although there has been a definite increase in fiber knowledge within the communications markets since I started in this industry, there is still a lot to be learned.
We are still seeing many of the same issues in the field that we saw 10+ years ago. Some of the most common things we find or hear about should not still be happening today. Why do these misconceptions persist? What are the big culprits?
Here are a few anecdotes I STILL hear from the field.
• "I just cleave fibers with a pair of scissors. That works fine."
• "There’s no need to clean connectors. I always pull them out of the bag directly from the manufacturer and they are ready to go."
• "Watch me strip off the cladding."
• "I still hand polish my SM APC connectors in the field."
• "My shirt cleans connectors just fine. ‘Field clean,’ so to speak!"
• "If I run over a length of cable with my chair, should I tell someone?"
That last comment is from a woman who worked for a cable assembly house. Once she understood the basics mabout how fiber transmits light, and what the cable can and cannot withstand, she realized that she might be damaging some products when her chair rolls over a length of cable that she is terminating. Knowledge sure is powerful!
After all these years of fiber deployment, all the internal and external training classes, all the articles, webinars, and trade show seminars, there are still a fair number of people who lack a real understanding of how fiber optic links work. We find that some students come to class with limited experience or time in the field. Yet, they consider themselves quite knowledgeable because they have been doing something for more than a year.
Sure, there are many great fiber splicers, installers, and engineers out there who know a lot. There are also many who do not.
Here are a few thoughts on why these common problems stick around.
• If training is done only on the job, bad habits and short cuts can be passed along.
• People can develop a feeling of expertise because no one has corrected them. Their errors have been small enough to go unnoticed in a lower speed network.
• Generally, doing things the way it "has always been done" is easier than change, and many people simply don’t speak up.
• Companies provide their staff with limited training that is often only product-specific rather than general knowledge, process, and/or technology training.
• Training is not always followed by practice — so much of the knowledge is lost before it can be applied and ingrained.
Given this, how can you avoid some of the most common field problems? The first step is to identify what they are, what to do, and what NOT to do.
Top Problems and Remedies
#1: Using dirty or damaged connectors. As someone who has been singing this tune for ages, I continue to be astonished that people do not properly clean their connectors before plugging them in. I don’t mean rubbing it on a shirt — and don’t get me started about people who think they can rub the end with their finger!
Today’s high-speed networks will no longer tolerate any dirt, oils, or residue, on connectors. The added loss, and especially the added reflections, will start impacting network performance.
The first step to remedy this is to require your staff to properly clean and inspect connectors before mating and before plugging into their test equipment ports. You have no idea how many people bring their equipment to a class to ask for help because it is not working right, and we find the connector at the source to be a complete mess.
There is good news however. We recently surveyed our newsletter readers regarding connector cleaning and inspection, and the results make me hopeful! (See Figure 1.)
Figure 1. Results from surveys on connector cleaning and inspection.
#2: Avoid bending losses. There are so many places where we unknowingly introduce an excessive bend or pinch point. (See Figure 2.) In training, we teach students about microbends and macrobends to provide an understanding of what can go wrong. It is easy to reduce the likelihood of bending issues by focusing on proper routing, handling, or securing, of fibers and cables.
Figure 2. Fiber, tubes, cables can be pinched or excessively bent. Bends and pinch points in installed optical fibers. Note the light leaking from the fiber in the tube.
Problems generally happen when dressing out splice trays or entering patch panels. Damaging bends can be caused by pulling too tightly on a tie wrap, or closing a cover on a stray fiber loop, or not managing slack properly.
#3: Be aware and be careful. Use the right hardware, clips, straps, and fiber management, both in and out of closures, racks, panels, etc. Follow manufacturer’s instructions on how much jacket to strip back, how much furcation is needed, and fiber strip lengths. These have been provided for a reason: so that everything can properly be stored in the fiber management hardware provided.
#4: Don’t connect mismatched connectors. Sure, this is an easy one, but we still see it happen: don’t plug an SC UPC connector into an adapter that has an SC APC connector on the other side. (See Figure 3.) And don’t use a multimode adapter to mate single-mode connectors. There is a reason that those adapters cost less than the SM versions. The sleeves have less tight tolerances, and the material is a bit less rigid. This leads to less precise alignment of the ferrules, and that creates more potential loss.
Figure 3. When mating an UPC connector to an APC connector, the resulting air gap causes excess reflection and loss.
#5: If you troubleshoot networks and outages, consider getting an optical fiber identifier (OFI) for your tool box. OFIs can determine if there is traffic on your fiber and tell you from which direction it is coming. (See Figure 4.) They can also pick up tones if you are working on network mapping or trying to identify what is connected to what. (Which leads us to another common field issue: poor record keeping — but we will save that for another discussion.)
Figure 4. An optical fiber identifier with screen displays that show traffic and tone detection.
The best advice on OFIs is to do your homework before buying one. The price points vary quite a bit, but so does the performance. Vendors specify what type of fibers and cables they can "read". If you have access to bare fiber, you can probably use many different options. If you need to check dark 900µm fibers or 2mm or 3mm simplex cables, you might want to test out some options. If you use a lot of bend insensitive fibers, there are fewer choices. I suggest you ask your favorite vendor(s) for a demo unit to try out before buying.
These are just a few of the many potential problems in the field. Remember: knowledge is power — and it can help keep your rework and troubleshooting costs down too!
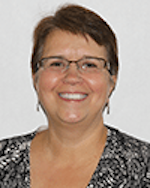