Latest from FTTx/Optical Networks
Infrastructure Advancements in the Outside Plant —
Planning fiber networks a decade ago was relatively simple as these systems were built largely for a single purpose, and the purpose was straightforward: transmit signals in a landline-and-desktop-computer world.
With evolving mobile applications and always-on consumer needs, the network infrastructure enabling these applications and services must also evolve. It is increasingly clear that the appetite for bandwidth will be satisfied only by positioning fiber ever closer to where the people are — whether they are residential subscribers, or in a school, small business, or large office building.
Backhaul Demands
As network operators plan these deep-fiber deployments today, they can avoid costly overbuilds in the future by considering the technology advances (ITU and IEEE standards) needed to deliver symmetrical 10 Gbps and 25 Gbps speeds. While some of the uses for future networks remain unknown, what is given is that mobile backhaul will be critical as 4G densification amps up and 5G preparation becomes a reality.
Balancing the needs of mobile backhaul and end-user applications requires a new kind of flexibility in the network. This requirement is a catalyst for evolving product features in the outside plant. What were once options have become standard features, like full pass-through capability in distribution cabinets. This particular feature enables operators to bypass splitters so individual subscribers or businesses can be served with a dedicated circuit. But the network evolution isn’t stopping there.
Figure 1. Small, pole-mountable multiuse cabinets enable flexible end-user delivery.
Trends toward systems that can support not only pass-through capability but a mix of traditional centralized split as well as distributed split architectures allow for individual end-user bandwidth delivery. This individualization enables highly customized delivery for today’s bandwidth needs while keeping an eye on tomorrow.
Keeping an eye on the horizon is one thing operators and manufacturers have in common. Both also pursue opportunities to reduce costs across the network. To reduce civil costs, for example, new pole-mountable, small multiuse cabinets and efficient below-grade solutions are gaining acceptance. (See Figure 1.) Operators are even reusing existing handholes to do more with what they have.
To further optimize their infrastructure investments, operators increasingly prefer compact, flexible, robust solutions. Recent manufacturing and deployment innovations address those concerns, making fiber deployment cost-effective and within reach for all operators — regardless of their network size.
Deploying Higher Fiber Counts
To affect the needed increase in bandwidth demand, fiber deployments aren’t just moving closer to the subscriber. They are driving higher fiber counts in the outside plant. At the same time, 4G and now 5G contribute to a surge in the number of cell towers across serving territories. But in the access network, it can be very expensive to add additional fiber capacity — especially in underground deployments.
Micro cable was born 15 years ago in Europe, where regulation prohibits much of the aerial infrastructure deployed in the rest of the world. Now micro cable is gaining appreciation and adoption in the US and Canada for its cost-effective, unobtrusive deployment possibilities.
Following a traditional loose tube design, micro cable is highly engineered for installation specifically within microduct, whether it is deployed into a narrow slit alongside a roadway or run through a distribution network.
Because microduct provides the protection in these deployments, micro cable can achieve much higher density by eliminating some of the robustness that traditional loose tube cable needs in direct-buried and lashed applications. A higher portion of a micro cable’s outer diameter comes from fiber density, since this cable design is optimized for light-tension duct jetting.
Figure 2. Micro cable is almost 50% smaller than traditional loose tube cable.
In Figure 2, notice the size difference between a traditional loose tube and a micro cable design. Both have 144 fibers, but the micro cable is almost 50% smaller.
Where micro cable really delivers value is in combination with scalable microduct systems. Together, they enable high-density deployments and the ability to add capacity when the network needs to grow. Figure 3 shows a 144-fiber loose tube cable on the far right installed in 1.25-in duct. In the same footprint, over 1,000 fibers can be deployed in microduct using 144-fiber micro cable. And the capacity gains are even greater when using 288-fiber micro cable.
Figure 3. Same footprint: 144 fibers with loose tube cable vs. 1,512 with high-density micro cable.
These high-density micro cables take the innovation in cable construction one step further. Whereas 250 μm is the typical loose tube fiber diameter, high-density micro cable delivers the same optical specifications in a new 200 μm fiber. The only difference is a smaller coating around the fiber core and cladding, enabling fibers to be packed more densely. Since the core and cladding size of 200 μm and 250 μm fiber is the same, they are fully compatible and can even be spliced together.
Increasing Deployment Velocity
Along with higher fiber counts, fiber-deep networks translate to increases in the number of times that deployed cable is accessed. While the loose tube cable design has long served the telecommunications industry, recent innovation around its jacket and binding is significantly reducing cable access times.
The traditional approach to accessing cable involves hook blades and ripcords to split the jacket. At times, especially in armored cable, ripcords break as they are pulled through the cable’s exterior. Through manufacturing advancements, the ripcords have been removed altogether.
Replacing them are cable jackets with seams on both sides, allowing the cable to be peeled apart by hand much like you would peel a banana. This feature improves access over traditional methods and reduces the need for sharp tools like seam rippers.
These sewing instruments are common in technicians’ kits for their ability to sever binding yarn wrapped around buffer tubes. This bundling of buffer tubes serves no purpose outside of manufacturing, but with technicians having to remove binding yarn with sharp objects every time a cable is accessed, it does contribute to labor costs.
Fortunately, recent advancements in cable manufacture have eliminated the need for traditional binder yarns. Combine these manufacturing advancements with peelable jackets, and improving access times for technicians. Add up the time saved on cable access, and operators have a tangible impact on deployment velocity.
Speaking of labor, improved cable designs make installations and upgrades so easy that time savings are independent of skill level, training, or experience. Our internal studies show that the difference in access times between experienced and novice technicians is negligible (and much quicker for both).
Seizing the Opportunity
To deliver the strong, reliable networks that connect homes, businesses, and people wherever they are, operators are deploying fiber — and lots of it — ever closer to subscribers. Getting the fiber in place is essential for operators to offer the services and applications their customers expect, but how that fiber is deployed will impact the network’s bottom line. Every fiber-deep deployment is an opportunity to leverage innovations in fiber optic hardware and cable to scale effectively with reduced cost over the life of a network.
Derek Whitehurst is Director, Global Applications Marketing for Corning. He has more than 24 years of experience in the industry, currently focusing on long-haul, metro, wireless backhaul, and outdoor cable. For more information, please email [email protected] or visit www.corning.com/opcomm.
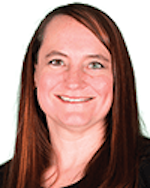