Latest from FTTx/Optical Networks
Best Practices for Selecting PON Components for Harsh Environments
Passive Optical Networks (PONs) are helping service providers around the globe reduce fiber optic network build costs by pushing the optical components further into the outside plant (OSP) network and thus eliminating the need for climate-controlled hubs powered by electricity. A PON reduces the amount of fiber and central office equipment required when compared to point-to-point architectures and generally provides higher bandwidth and better security than traditional copper-based access networks.
However, providers need to ensure that the PON components they use can handle the harsh environments and extreme temperatures (and temperature swings) of an OSP network. Selecting high-quality, reliable, tested components is the only way to ensure the performance and dependability needed in today’s market.
Prior to Fiber-to-the-X (FTTx) deployments, the majority of optical components were installed in buildings and enclosures that had a controlled environment. Today, passive components can be deployed above-grade in pedestals and below-grade in splice closures or terminals in vaults, mounted on poles, hung in aerial closures, and in outdoor enclosures on the exterior of a building. In an OSP environment, these elements could see extreme temperatures depending on their geographic location; in the desert of Arizona and Mexico, where it can reach 120F/49C degrees and higher, or in Fairbanks, Alaska, where temperatures can get below -40F/-40C. Passive optical components need to be able to perform optically and mechanically in these extreme elements. Another element to worry about is rapid temperature change, which can cause a catastrophic failure to inferior optical components.
4 Key Factors to Consider
There are several key factors to consider when considering components for deployments in harsh environments. These include:
Factor 1. Accreditation and certification to known testing plans.
Factor 2. Understanding requirements for quality fiber optic cable.
Factor 3. Understanding requirements for reliable fiber optic termination.
Factor 4. The environmental and mechanical requirements of quality passive optical components.
Let’s take a look at each of these factors as they relate to a successful PON deployment.
Factor 1. Accreditation and Certification
Accreditation and certification to known testing plans is critical in evaluating PON components for quality and reliability. Some of the most trusted testing plans for fiber optic components comes from Telcordia Generic Requirements (GR), which are complete testing plans that provide guidance about features that are necessary or desirable for specific products, and presents performance criteria that these products should meet. For PON buildouts, these include:
• GR-20 and GR-409 — Fiber optic cables
• GR-326 — Fiber optic cable terminations
• GR-1209 and GR-1221 — Optical components such as splitters, WDM, CWDM, DWDM and Circulators
Factor 2. Quality Fiber Optic Cable
When designing a quality network, starting with a quality fiber optic cable is key. Some of the important requirements within GR-20 and GR-409 are cable construction, cable markings and packaging, cable materials, jacket requirements, mechanical requirements, environmental requirements, electrical protection requirements, and optical performance requirements. The mechanical, environmental, and optical performance requirements focus on areas that can be most affected by extreme temperatures.
Factor 3. Reliable Fiber Optic Termination
Termination of fiber optic connectors on to fiber optic cable has become a very important part of the OSP fiber optic network, so the reliability of the termination on the cable is key. As noted in the PON design, an increasing number of components are being deployed in the field in uncontrolled environments that will see extreme temperatures and rapid temperature change. It’s not unlikely for the temperatures inside of some enclosures such as an above-ground pedestal or an aerial terminal to be 10 to 20 degrees warmer or cooler than the outside air.
Telcordia GR-326 refers to the requirements for single mode optical connectors and jumper assemblies, including multi-fiber cables that could be terminated directly in a cross-connect cabinet, or inside of a SmarTerminal or pedestal. It would also include the simplex and duplex patchcord jumper assemblies that are used in outdoor closures, at an ONT, or when terminated on an optical component like a splitter or WDM.
(For the 3 key details to make your connection count, see the sidebar "Connection Adaptations" on page 28.)
Factor 4. Quality Passive Optical Components
When testing optical components that are terminated with connectors, they go through the full GR-1209 and GR-1221 requirements with the terminations included. This will subject the complete assembly to the temperature extremes of the test requirements.
GR-1209 Requirements are designed to demonstrate the short-term operational performance of passive optical components and were chosen to be compatible with those specified in GR-1221-CORE, which is used to demonstrate the long-term reliability of components. This is done to minimize the use of 2 different sets of samples to accomplish short-term performance and long-term reliability evaluations. Key factors to quality passive optical components include:
Insertion Loss: When it comes to splitters and WDMs there can be a significant amount of light or power loss as compared to the fiber itself or the terminations used on fiber cables. Typical single mode cable has a dB/km loss of 0.35dB at 1310nm and 0.25dB at 1550nm. Typical connectors have a loss of 0.35dB, however Clearfield will guarantee a maximum insertion loss of 0.20dB per connector with a typical loss of 0.15dB. Using premium optical components with premium low-loss terminations reduces total insertion loss budget, and allows further extension of the fiber network.
Return Loss: This is the percentage of power reflected back from a particular point in a light path. It is measured as a negative decibel (dB). Reflections can be caused by any impurities in the core or cladding, micro-bends or macro-bends, and any splices or terminations. A quality optical component should have minimal return loss.
Uniformity: This is the maximum insertion loss difference between one input or common port and all the output ports. The tighter the uniformity, the better. This helps to ensure that the transmission power at each output port is within a specified range, allowing for simpler network design.
Optical splitters deployed for a WDM PON system have additional performance criteria such as Optical Bandpass, Wavelength Isolation, Wavelength Stability, Directivity, and Polarization Dependent Wavelength (PDW).
GR-1221 Requirements outline environmental and mechanical test requirements to ensure long-term operational performance. The reliability test requirements include:
• Mechanical Integrity tests such as Mechanical Shock, Vibration, Thermal Shock, and Fiber Integrity. These tests are designed to ensure reliable optical performance when subjected to common conditions during storage, transportation and installation.
• Endurance tests including High Temperature Storage (Dry), High Temperature Storage (Damp), Low Temperature Storage, Temperature Cycling, Cyclic Moisture Resistance, Airborne Contaminants, Water Immersion, and Salt-Fog. The tests simulate an accelerated aging effect to expose the component to weaknesses that may come about during the estimated lifetime of an optical component. The moisture coupled with the thermal cycle temperature levels will have an effect within the optical component, especially the epoxy which provides a high level of structural integrity to the waveguide chip, ferrule and filter adhesion in the final package.
When it comes to designing an optical network and selecting the components that will be used during the build, providers need to do their research and select high-quality, reliable components. If an optical component fails in the field, it would cause unexpected outages and could affect numerous customers at once. It would then require high-level technicians to troubleshoot and repair/replace the failed components, creating unexpected (and unbudgeted) expenses. The less-expensive component that has not been fully qualified will most likely cost more in repairs in the long run.
[toggle title=”Connection Adaptations” load=”hide”]There are 3 main things that contribute to a quality termination:
#1: The connector components themselves. Details to keep in mind include:
• Ferrule: Quality Zirconia ceramic material, precision tolerances with tight concentricity for improved fiber core alignment keeping insertion loss to a minimum, high strength and durability for repeated matings, resistant to aging and chemicals, high pull out force from holder.
• Ferrule Holder: Non-corrosive material resistant to salt spray and chemicals, tight tolerance, high ferrule pull out force.
• Spring: Consistent spring force that meet the conditional limits specified by the TIA/EIA FOCIS documents, non-corrosive material resistant to salt spray and chemicals.
• Housings: Non-corrosive metal and plastic materials resistant to salt spray and chemicals, especially ones found in the Immersion/Corrosion test in GR-326 4.4.4.5.
• Strain Relief and Boots: Reliable high strength strain relief pull out force of fiber and jacket retention, bend limiting boot, non-corrosive metal and plastic materials resistant to salt spray and chemicals especially ones found in the Immersion/Corrosion test in GR-326 4.4.4.5.
#2: A controlled, repeatable termination process. Termination of fiber optic cable in a controlled manufactured environment is strongly recommended. Factory-terminated assemblies and pre-terminated optical components are best. Using a plug-and-play design will help to eliminate failures due to termination or component failure in extreme environments. Other factors that can impact the termination process include:
• Cleanliness. Contamination during the process reduces consistency and repeatability of the process.
• Cable Preparation and Stripping. Using high-quality cable preparation and fiber striping tools can help to eliminate the chance of fractures to the fiber unseen by the human eye. A nick to the cladding of the glass can later become a large fracture causing the fiber to potentially break. This would typically show up during the GR-326 thermal cycle test. The temperature cycle reaching -40C to +85C for 21 cycles over 168 hours will stress the fiber and most likely cause fiber damage or catastrophic failure.
Another important detail is the cable and fiber strip length. There needs to be the right ratio of fiber length to Kevlar length for that specific connector. If the fiber is prepped short with excess slack of Kevlar, this could allow the jacket to pull back from the connector, putting all the stress on the fiber itself and possibly breaking it.
• Epoxy Curing. The Epoxy can make or break a quality termination suitable for outside plant applications. The slightest foreign chemical or particles on the glass fiber or inside the ferrule can reduce the adhesion properties of the epoxy to the fiber and the ID of the ferrule. If the adhesion bond between the glass and ferrule are not adequate, the fiber could move in relation to the ferrule during temperature cycling. This goes for connectors in the field as well. As they are subjected to extreme temperatures and due to the expansion and contraction of the different materials, fiber can pull back from the end face, causing increased insertion loss or reflections.
Another issue that is often overlooked is air bubbles or voids of no epoxy inside the ferrule and ferrule holder when the fiber is terminated. A bubble or pocket of air near the back of the ferrule where the fiber is inserted can create havoc on a fiber termination. As temperatures increase or decrease, the air pocket puts stress on the fiber due to the indifferences of expansion and contraction of the ferrule to fiber potentially causing insertion loss or a possible catastrophic fiber break failure. Using premixed, degassed, frozen epoxy can help to reduce the chances of this happening.
• Cable Strain Relief. One of the most common failures for mechanical testing is not having enough cable strain relief to the connector. The vibration, flex, twist, impact and proof tests in GR-326 will determine if the cable jacket that is supposed to be secured to the connector is adequate. If the strain relief starts to fail, it will work its way out of the back of the connector and can expose the fiber itself. The Kevlar can also slip out from the crimp and then all the force is then applied to the fiber itself. Strip length is important; too much slack on the Kevlar could allow the cable to pull back on the connector, putting all of the strain on the fiber before the Kevlar slack starts to take on the load, causing the termination to fail.
#3: The intermateability of a connector. This assures that the product purchased from one vendor will function satisfactorily when intermated with a product manufactured by another supplier. The verification is basic dimensional requirements but does not determine the use of specific designs or materials. [/toggle]
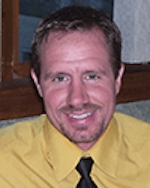