Latest from Home
Preventing Telecommunications Equipment Damage During Cleaning and Disinfection of COVID-19
We are all accustomed to computers being attacked by viruses, but we now face a very different type of attack. Due to Coronavirus Disease 2019, or COVID-19, increased emphasis is now being placed on how to reduce the risk of infection. The safety and health of employees and colleagues working in facilities is each operator’s top concern.
While Ericsson does not provide equipment cleaning services, we want to reach out to the industry and provide some useful information regarding cleaning and disinfecting of telecommunication facilities.
• This is important for the safety of our people.
• It’s also critical because if not done correctly, there could be short- or long-term damage to telecommunications equipment at a time when the network is in high demand.
InvisiLight® Solution for Deploying Fiber
April 2, 2022Go to Market Faster. Speed up Network Deployment
April 2, 2022Episode 10: Fiber Optic Closure Specs Explained…
April 1, 2022Food for Thought from Our 2022 ICT Visionaries
April 1, 2022In the recent past, equipment cleaning procedures were used to deal with the Anthrax attacks. However, Anthrax is bacterial and COVID-19 is viral. Thus, the chemicals to clean equipment today may be different.
Disinfecting electronic equipment (data centers, network facilities, customer POP, etc.) with gaseous chemical agents or solvents in response to COVID-19 could have an adverse effect on some critical electronics.
We saw this in field measurements made after the Anthrax attack on government facilities in 2001. At that time, the disinfectants used were very corrosive. We learned this via an ion chromatography analysis. We realized that to determine the best course of action for a specific situation, the professionals spearheading the cleaning must have a thorough understanding of different metals and plastics, and of how they respond when exposed to cleaning agents.
For convenience, there may be an attempt to disinfect large facilities by fumigating with gasses such as Chlorine dioxide. This will draw the disinfecting agent into electronic equipment, and could result in corrosion of many types of metals. This method of disinfection should be avoided unless an examination of alternative methods deem it a necessity.
Wiping with Clorox® Bleach (active ingredient: sodium hypochlorite) can be used in some instances to clean surfaces. These cleaners are also corrosive to many metals, and their use may require a secondary clean-up with a mixture of distilled water and alcohol to prevent or reduce corrosion damage.
Alcohol is a preferred disinfecting solution for sensitive electronics. A solution of alcohol can safely be used on equipment exterior surfaces, screens, and keypads. At the concentrations needed for effective disinfection, flammability is a concern. Alcohol should not be used near open flames or other potential sources of ignition.
2 Steps Are Best
The following is a two-part cleaning that may be required to prevent damage.
STEP 1. Equipment Disinfection and Cleaning Analysis
The first item to check is:
What chemicals are being used to disinfect?
• Some chemicals may be good at disinfecting but can damage network equipment.
• Common disinfecting agents such as chlorine dioxide gas, halogenated agents, and certain detergents leave behind acidic or caustic residues that are highly corrosive to electronics and associated metals.
• The means of application must also be checked. Certain gaseous discharge processes may create thermal shocks due to low temperatures at the point of agent discharge.
Review and evaluate decontamination chemicals and procedures.
• Assess the proximity and likely impact on nearby telecommunications and electronic systems.
• Assess the potential impact on other building infrastructure such as air handling systems, fire-safety systems, building control and alarm circuits, and wiring.
• Develop guidelines to ensure that disinfecting processes have minimal impact on nearby equipment.
o Include a secondary cleaning for removal of corrosive residues if needed.
STEP 2. Post Disinfecting Chemical Analysis and Mitigation
Perform on-site chemical sampling and analysis to determine the level of corrosive films on critical equipment, and to develop procedures to safely clean these residues when needed.
• Typical analyses include surface sampling with ion chromatography to quantify contaminants, and the use of scanning electron microscopy with energy dispersive spectroscopy to identify elemental constituents. Observed contaminant levels are compared with established industry guidelines for restoration of electronic equipment.
o If needed, a cleaning protocol is then developed, and additional sampling is performed post-cleaning to ensure cleaning effectiveness.
Check the proximity and the sensitivity of operating telecommunications and other electronic equipment to the targeted area.
• If warranted, equipment may need to be temporarily compartmented and protected.
• If equipment must be exposed to disinfecting chemicals, a subsequent cleaning to neutralize corrosive residue may be needed.
It is essential that network operators provide consultation to firms who hire cleaners, to those who supervise the cleaners, and to those who do the actual cleaning.
Operators will need to provide all involved parties in cleaning the proper procedures to minimize the impact on sensitive telecommunications equipment, as well as general safety procedures for working around sensitive equipment.
Like this Article?
Subscribe to ISE magazine and start receiving your FREE monthly copy today!
A useful site to get more information on the materials used is https://www.epa.gov/pesticide-registration/list-n-disinfectants-use-against-sars-cov-2
Please contact us if you need any assistance in dealing with the cleaning of network equipment. Email [email protected] or visit https://www.ericsson.com/en. We can provide assistance in reviewing, or developing, methods and procedures for cleaning.
This article is co-authored by Ernie Gallo and Randy Schubert
Randy Schubert is Project Manager / Technical Lead at Network Infrastructure Solutions, a division of Ericsson, Inc. He has more than 25 years of experience in hardware disaster recovery and network reliability. For more information, email [email protected] or visit www.ericsson.com.
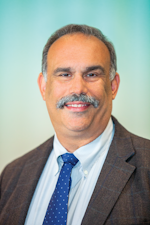
Ernie Gallo | Director at Network Infrastructure Solutions, a division of Ericsson, Inc.,
Ernie Gallo is Director at Network Infrastructure Solutions, a division of Ericsson, Inc., and an IEEE C2 National Electrical Safety Code - Committee Member, Subcommittees SC2, SC4, SC5, and SC8. He has more than 40 years of experience in outside plant products, requirements, deployment, and electrical safety codes and standards such as the NEC and NESC. For more information, please email [email protected] or visit https://www.ericsson.com/en. Follow Ericsson on Twitter @ericsson.
For more information, please visit https://standards.ieee.org/products-programs/nesc/ to learn more information about the NESC and NESC Products. Follow the IEEE SA on Twitter @IEEESA. We welcome you to contribute to our efforts by joining the NESC.